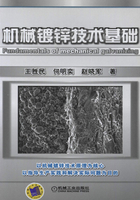
2.4 锌粉吸附、沉积的影响因素
2.4.1 温度、pH值对锌粉吸附、沉积的影响
机械镀锌一般在室温下操作,镀锌过程镀筒内浆料的pH值在镀锌开始时通常为1~2。随着锌层的逐渐形成,浆料发生一系列复杂的物理、化学变化,导致镀覆结束时浆料的温度升高5~8℃,pH值升为3~5。由此可见,形成镀层时镀筒内浆料温度、酸度的变化与镀筒内锌粉、工件、各添加物质有着紧密的联系。
1.温度对锌粉吸附沉积的影响
温度越高,越有利于促进镀液浆料中前述式(2-5)~式(2-9)反应的进行,但这并非对镀层的形成过程有利。例如,当温度为45℃、65℃时,因为镀液中式(2-7)、式(2-8)反应加剧,致使锌粉在瞬间聚集、吸附,在工件表面形成粗糙、颗粒较大的吸附点,吸附沉积不均匀,甚至锌粉聚集成尺寸较大的锌-锡团,游离于镀液中,因颗粒尺寸较大而不能有效地被工件表面吸附、沉积。更重要的是,随着镀液温度的提高,对式(2-6)反应的影响较为显著。在室温下,pH值为1.5的酸性水溶液环境中,锌粉颗粒因式(2-6)反应的发生能聚集成藻团,但挥发皿底部残留有少量游离状锌粉颗粒,在辅助机械搅拌的情况下锌粉颗粒全部吸附团聚,锌粉团聚后的藻团尺寸约为0.5~1mm(见图2-30)。当温度为45℃时,pH值为1.5的酸性水溶液环境中,锌粉颗粒因式(2-6)反应加剧而快速发生团聚,挥发皿中无游离锌颗粒残留于挥发皿底部,机械搅拌后锌粉团聚藻团尺寸约为1~3mm(见图2-31)。当温度为65℃时,pH值为1.5的酸性水溶液环境中,锌粉颗粒因式(2-6)反应加剧快速发生团聚,挥发皿中无游离状锌颗粒残留于挥发皿底部,机械搅拌后锌粉团聚藻团尺寸约为2~4mm(见图2-32)。由此可见,温度能加速锌粉颗粒的团聚。
图2-30 室温下锌粉颗粒在pH值为1.5环境中的吸附团聚情况
a)搅拌前 b)搅拌后
图2-31 45℃时锌粉颗粒在pH值为1.5环境中的吸附团聚情况
a)搅拌前 b)搅拌后
图2-32 65℃时锌粉颗粒在pH值为1.5环境中的吸附团聚情况
a)搅拌前 b)搅拌后
虽然温度能加速锌粉颗粒的团聚,但要综合考虑温度对式(2-7)反应的影响。如果温度过高,导致式(2-7)反应快速进行,锌-锡团聚体因尺寸较大不能及时在工件基体表面吸附、沉积,反而在镀液中产生锌球(见图2-33)。ICP-AES分析表明,这种锌球定量溶解后,溶液中锌、锡、铁三种金属元素的质量浓度分别为1099.0μg/mL、54.74μg/mL、11.06μg/mL。锌球的X射线衍射图谱如图2-34所示。分析图2-34可知,锌球中含有锌、锡、铁三种单质,没有发现锌、锡、铁之间的化合物、固溶体等合金物相。结合ICP-AES分析结果,锌球中锌、锡、铁金属单质的质量比为94.35∶4.70∶0.95,可见锌单质是锌球的主要物相组成。由此可以推断,温度较高时,式(2-7)反应加剧,锌-锡藻团快速生成并不断长大,因尺寸较大而游离于镀液之中。随着机械镀锌过程的镀层循环增厚,小的锌-锡藻团经不断长大、挤压、摩擦而成为锌球。这种锌球的主体是锌粉颗粒,锌球内部不存在玻璃丸。
因此,在机械镀锌工艺过程中,并非施镀温度越高越好,要具体情况具体分析。例如,我国北方地区,冬季生产车间内温度较低,可采用40℃左右的温水施镀。
图2-33 锌球的外观形貌
图2-34 锌球的X射线衍射图谱
2.pH值对锌粉吸附、沉积的影响
目前,机械镀锌工艺过程普遍采用的pH值为1~2。若pH值偏低,则镀液中式(2-6)反应激烈,锌粉的无益消耗大,甚至锌粉颗粒团聚较快、藻团尺寸较大或吸附成漂浮层浮在镀液表面而不能在基体表面吸附沉积;若pH值偏高,则镀液中式(2-6)反应缓慢,锌粉团聚速度较慢,甚至有大量游离态锌粉颗粒沉淀在镀筒底部,导致锌粉颗粒不能连续、有效地在基体表面吸附沉积。
2.4.2 非锌微粉和稀土对锌粉吸附、沉积的影响
1.非锌微粉对锌粉吸附沉积的影响
随着工件服役环境的苛刻,人们对工件的耐蚀性能提出了更高的要求,锌基复合镀层、合金化镀层也成为机械镀锌技术近几年发展的热点。例如,在机械镀锌过程中,人为添加铝粉制备锌-铝镀层,人为添加非水溶性纳米颗粒制备锌基纳米镀层。根据需要,这些外加颗粒可分为两类:①金属颗粒,这种颗粒能与锌粉协同沉积或部分协同沉积,形成的复合镀层能提高耐蚀性,例如铝粉;②微细非金属颗粒,这种微细颗粒基本不能与锌粉颗粒协同沉积,甚至不易自发在基体表面吸附沉积,主要依靠锌粉颗粒吸附沉积时的夹带作用沉积在基体表面,其主要作用是填充镀层中的空隙位置,提高镀层的致密度,例如PTFE、纳米TiO2。
(1)铝粉添加对锌粉吸附、沉积的影响 由于铝是一种较为活泼的金属,铝粉颗粒表面容易被Al2O3氧化膜覆盖,这使得铝粉表现出不同于锌粉的各种特性,特别是在水溶液中的润湿性和分散性远不如锌粉。当采用同传统机械镀锌相同的施镀条件时,铝粉在镀液中基本不发生润湿,而是漂浮在镀液表面,更不会吸附团聚,且添加酸(硫酸或盐酸)对铝粉基本没有作用(见图2-35)。当在镀液中添加铝粉活化剂对铝粉活化去除颗粒表面的氧化膜时,可以实现锌粉、铝粉的协同或部分协同沉积。例如,添加氟化钠的酸性环境中铝粉可以实现部分团聚(见图2-36)。因此,在机械镀锌时,添加合适的活化剂可以实现锌粉、铝粉的共同或部分共同沉积(见图2-37),但铝粉的有效利用率低于锌粉。
图2-35 铝粉在H2SO4+H2O中的团聚
图2-36 铝粉在H2SO4+H2O+NaF中的团聚
图2-37 锌粉+铝粉的共同吸附沉积
(2)纳米TiO2添加对锌粉吸附、沉积的影响 纳米TiO2不溶于水,在弱酸性环境中具有较好的稳定性。在机械镀锌过程添加这类粉体的主要目的是,使这些微细甚至纳米颗粒填充镀层中的空隙,提高镀层的致密度。这类粉体(如TiO2、PTFE)在镀液环境中基本呈现惰性,难以依靠活化剂使其表面活化,进而与锌粉颗粒协同沉积或部分协同沉积。例如,添加TiO2纳米粉体的吸附沉积过程主要是依靠金属锌粉吸附沉积时的夹带作用,使TiO2沉积到工件基体表面。因此,TiO2纳米粉体的有效利用率低,只有部分粉体沉积到工件表面或镀层中。在制备Zn-TiO2机械镀层时,当镀覆完成后,取出镀筒内镀液观察可发现TiO2有明显的残留(见图2-38)。
图2-38 镀液中残留的TiO2
a)沉淀前 b)沉淀过滤后
2.稀土对锌粉吸附、沉积的影响
传统的机械镀锌过程,金属锌粉聚集大约为0.5mm直径的藻团,在镀件表面分散成连续或不连续的薄层,可视为点状吸附沉积。通过试验模拟可以重现以上现象,如在挥发皿中依次加入水、无机酸、锌粉、活化沉积剂和工件,玻璃棒搅拌后待到静止状态观察。金属锌粉一般以粗大、松散的藻团吸附在工件表面(见图2-39)。同样情况下,如果加入适量的稀土金属盐溶液,蓬松藻团状的锌粉团变得细小,可视为面状均匀吸附(见图2-40)。值得注意的是,在加入稀土金属盐溶液后,锌粉在溶液中仍然聚集为藻团,只是此时的藻团直径减小,约为不加入稀土之前的1/3~1/2。由此可见,稀土具有细化锌粉藻团的作用。
图2-39 模拟加料时锌粉的吸附沉积
图2-40 模拟加料时加入稀土后锌粉的吸附沉积
两种吸附、沉积现象的规律如图2-41所示。以面状方式沉积的金属锌粉层,一般以大粒径颗粒吸附若干小粒径颗粒沿被吸附面铺展成薄层,在受冲击力作用的初期颗粒容易运动,发生小范围的位移相互填充间隙,形成较均匀的层体,然后将冲击力分散传递使颗粒逐步变形、镶嵌成层。点状吸附沉积时,颗粒形成小区域堆积团,由于堆积区域相对较厚,冲击力作用的初期在垂直于基面方向通过多层颗粒传递衰减较大,对颗粒层的运动、充填和铺展成层不利,堆积区域中易残留较大的间隙空间而形成疏密不匀的堆积层体,不利于后续冲击力的传递,进而影响到镀层中锌粉、层体的变形程度和镶嵌的紧密度。总之,面状吸附沉积在冲击条件相同时,形成镀层后的致密度和外观平整度高于点状沉积,加入复合稀土金属盐后可改变锌粉的富集特性,并改善吸附沉积特性,使其倾向于形成细小的藻团,趋于面状吸附沉积,最终使镀层平整、光亮、均匀性好。
图2-41 金属锌粉在镀件表面的吸附、沉积方式示意图
a)面状吸附 b)点状吸附沉积