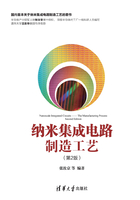
第2章 集成电路制造工艺发展趋势
2.1 引言
20世纪中叶以来,以电子计算机为代表的电子技术产品的不断革新使得社会的发展日新月异,社会的每个方面都产生了深刻的变化。集成电路产业作为技术革命的中心,是整个社会电子产品最不可或缺的要素。集成电路工业发展如表2.1所示[1]。
表2.1 集成电路工业发展趋势

从表2.1中可以看到50年来集成电路技术发展的巨大变化。集成电路工业在系统需求增长的推动下,如摩尔定律(大约每24个月芯片上集成元件的数量就翻一番)所描述的,密度和性能方面持续地和系统化地不断增长,持续降低的功能单位成本(cost per function,以往每年可降低约25%~29%),通过计算机、通信以及其他工业与消费电子的普及,从而极大地提高了经济生产力和人们的总体生活质量。这一切在很大程度上要求集成电路制造工艺不断发展。
集成电路制造工艺发展的直接动力来自于单位晶体管制造成本的不断降低和晶体管性能的不断提高的要求。
第一,增大晶圆的尺寸。这是降低制造成本最直接的方法。晶圆尺寸的增加意味着同样的工艺步骤能生产出更多的芯片,从而降低晶体管的成本。如表2.1可见,50年的发展,晶圆尺寸从25mm增加到300mm,目前450mm的设备正在研发当中。这一领域正在产生重大的技术进步,而半导体制造商与供应商正进行对话,以评定300mm和450mm晶圆的标准与生产力改进情况。对相关情况的经济分析也正在对研发投入、利润、投资回报和资助机制的分析和建议等进行检查。晶圆尺寸的增大需要对设备提出更高的要求,比如在均匀性(uniformity)方面。
第二,降低晶体管的几何尺寸(geometric scaling)。集成电路的几何尺寸在几十年中降低幅度达到500倍以上。这是降低晶体管制造成本和提高晶体管性能的最有效的方法。几何尺寸的降低,直接地增加了单位面积上的器件数目,从而降低芯片成本,同时提高了晶体管的电学性能,如能耗、速度等。而相对应地,几何尺寸的不断降低要求集成电路制造工艺也做出不断的改进。而当半导体行业演进到90nm技术节点或更小尺寸时,单纯的几何尺寸缩小,不能够满足晶体管的性能提高,需要一些其他的手段来提高晶体管的电学性能,例如等效扩充(equivalent scaling)。Equivalent scaling的目标,如通过创新设计、软件解决方案和创新工艺来提高性能,将在未来的十年引导半导体产业前进[2]。如图2.1所示[3],应力技术,高k栅介质材料/金属栅等创新工艺技术在90nm之后逐渐应用。

图2.1 集成电路制造工艺技术发展趋势
第三,“超摩尔定律”(More than Moore, MtM)。“超摩尔定律”的做法通常会让非数字功能(例如射频通信、电源控制、被动组件、传感器、驱动器)从系统板级转变到特定的系统级封装(SiP)或系统级芯片(SoC)的潜在解决方案,并最后进入叠层芯片系统芯片(Stacked Chip SoC, SCS)。这里,也需要一些创新的集成电路工艺技术,如硅通孔技术(Through Silicon Vias, TSV)。
当集成电路在45nm技术节点或将来更小尺寸时,硅CMOS器件的微缩(scaling)将产生巨大的技术挑战及其相对应的解决方案。本章将重点结合微缩下的技术挑战,探讨集成电路制造工艺发展趋势。本书的第3~11章将对具体工艺进行详细讨论。