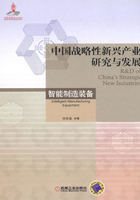
5.2 智能机床的关键技术与主要功能
5.2.1 智能机床的关键技术
1. 装备运行状态和环境的感知与识别技术
装备运行状态和作业环境的实时感知与识别是智能制造装备的必备功能。新型传感技术和RFID识别技术、高速数据传输与处理技术、视觉导航与定位技术等都是智能技术研发的热点。RFID和传感器结合与集成不仅具有感知与识别功能,还有传输和联网功能。数控机床和机器人的各种感知功能越来越丰富,并组成无线传感网络和嵌入式互联网。
智能机床的感知与识别技术面临如下重大挑战:
1)加工过程复杂、环境恶劣的要求。负载、温度、热变形和应力应变的实时高精测量,零件的高精高效的在线测量,以及装备性能劣化的实时感知等亟需新型传感技术和识别技术的突破。
2)装备的自律控制要求。由于感知对象的多样性和多维性,基于视觉等多源信息的三维环境建模和图像理解能力亟待提升,高速图像识别、运动图像的去抖/去模糊能力有待增强。
3)感知系统组网要求。装备的感知和识别系统具有高精高速数据传输、安全处理和容错能力,异构信息无缝交换能力。
就智能机床而言,其感知与识别技术要到达的主要目标是:
1)新型传感技术。突破高灵敏度、高精度、高可靠性和高环境适应性的传感技术,采用新原理、新材料、新工艺的传感技术,完善微弱传感信号提取与处理技术,光学精密测量与分析仪器仪表。
2)识别技术。低功耗小型化RFID制造技术,超高频和微波RFID核心模块制造技术和装备,完善基于深度的三维图像识别技术,物体缺陷识别技术。
3)高速实时视觉环境建模、图像理解和多源信息融合导航技术,力/负载实时感知和辨识技术,应力应变在线测量技术,多传感器优化布置和感知系统组网配置技术。
2. 性能预测和智能维护技术
在复杂的制造环境下,性能预测和智能维护是装备可靠运行的关键,为此需要提高监控的实时性、预测的精确性、控制的稳定性和维护的主动性。面向复杂工况的状态监控技术和装备性能预测技术等是当今制造装备研发的热点,已开发了初级的智能化产品和功能模块,如振动监测模块、刀具磨损/破损监控模块等,其功能和智能水平尚需进一步提高。
智能机床的性能预测和智能维护技术面临如下挑战:
1)监测信号与运行状态间存在复杂的关系,难以实时准确地表征运行状态和加工状态的重要特征。
2)复杂环境中系统整体功能的安全评估技术的研究刚刚起步,寿命预测技术研究仍不成熟。
3)装备性能演化机制的研究刚刚起步,装备性能指标体系尚待完备,其性能指标与制造过程状态特征的映射关系有待深入研究。
性能预测和智能维护技术要到达的目标是:
1)突破在线和远程状态监测和故障诊断的关键技术,建立制造过程状况(如振动、负载、热变形、温度、压力等)的参数表征体系及其与装备性能表征指标的映射关系。
2)研究损伤智能识别、自愈合调控与智能维护技术,完善损伤特征提取方法和实时处理技术,建立表征装备性能、加工状态的最优特征集;最终实现对故障的自诊断自修复。
3)实现重大装备的寿命测试和寿命预测,对可靠性与寿命精确评估。
3. 智能工艺规划和智能编程技术
数控机床的加工工艺规划与数控编程应综合考虑机器结构、工件几何形状、工艺系统的物理特性和作业环境,优化加工参数和运动轨迹,保证加工质量和提高加工效率。而现有编程系统主要是面向零件几何形状的编程,没有综合考虑机床、工装和零件材料的特性等,不能适应加工条件、应力分布、温度变化的不确定性。实现智能工艺规划和智能编程还需要逐步积累专家经验与知识,建立相应的数据库和知识库。
智能工艺规划和智能编程技术面临如下挑战:
1)由于机床的机械结构十分复杂,系统刚度和应力分布对位姿的依赖性,界面行为具有不确定性。机电液的复杂耦合关系造成了复杂的多场耦合问题,要建立精确的全功能和全性能工艺系统模型仍有一定的困难,需借助虚拟现实环境,进行模拟与仿真。
2)构建加工工艺数据库及工艺参数优化专家系统,需要进行大量的实验。实现工艺数据库与工艺系统模型的集成、定性知识与定量知识的融合与推理还面临一定的困难。
3)专家经验与计算机智能的融合技术作为工艺决策的重要基础,有待完善,加工工艺系统的自治配置和自治运行仍比较困难。
智能工艺规划和智能编程技术的预期目标是:
1)深入研究工艺系统的各子系统之间的复杂界面行为和耦合关系,建立工艺系统和作业环境的集成数学模型及其标定方法,实现加工和作业过程的仿真、分析、预测及控制。
2)建立面向典型行业的工艺数据库和工艺知识库,完善机床的模型库,逐步积累专家经验与知识,实现工艺参数和作业任务的多目标优化。
3)完善专家经验与计算智能的融合技术,提升智能规划和工艺决策的能力,建立规划与编程的智能推理和决策的方法,实现基于几何与物理多约束的轨迹规划和数控编程。
4. 智能数控系统与智能伺服驱动技术
数控机床的智能化也反映在数控功能的不断丰富和提升,如视觉伺服功能、力反馈和力/位混合控制功能、振动控制功能、负荷控制功能、质量调控功能、伺服参数和插补参数自调整功能、各种误差补偿功能等。伺服系统PID参数的快速优化设置问题、各轴伺服参数的匹配和耦合控制问题尚待进一步解决。
智能数控系统与智能伺服驱动技术面临如下挑战:
1)精度达纳米级,加速度超过10g的精密、高速、高加速运动控制技术;视觉伺服、视觉精密定位技术;重载、大惯量条件下的快速动作响应与精度控制技术。
2)切削过程中的切削力、热、振动对加工精度和表面质量的影响机制和刀具的磨损机理较为复杂,难以建立精确预测模型和提出合理的调控策略。
智能数控系统与智能伺服驱动技术的预期目标是:
1)完善智能伺服控制技术、运动轴负载特性的自动识别技术;实现控制参数自动优化配置;实现多轴插补参数自动优化控制;实现各种误差在线精密补偿;实现面向控形和控性的智能加工;基于智能材料和伺服智能控制的振动主动控制技术。
2)完善视觉感知和视觉伺服功能、力反馈和力/位混合控制功能;突破基于伺服驱动信号的实时防碰撞技术、非结构环境中的视觉引导技术,实现自律加工。
3)运用人工智能与虚拟现实等智能化技术,实现基于虚拟现实环境的智能操作,发展智能化人机交互技术。
5.2.2 智能机床的主要功能
1. 智能执行功能
智能机床在加工过程中,具有集自主检测、智能诊断、自我优化加工行为、远程智能监控为一体的执行能力,总结和分析智能机床的各种执行智能功能需求,具体功能如下:
1)负载自动检测与NC代码自动调节功能。
2)主动振动检测与控制功能。
3)刀具智能检测与智能使用功能。
4)工件加工状态与进度提取功能。
5)辅助装置低碳智能控制功能。
6)误差智能补偿功能(含热误差和几何误差补偿)。
7)防碰撞控制功能。
8)在线质量检测与控制功能。
9)自动上下料功能。
10)加工过程能效监测与节能运行功能。
2. 智能准备功能
智能机床在加工任务准备时,应具有在不确定变化环境中自主规划工艺参数、编制加工代码、确定控制逻辑等最佳行为策略能力。
1)数控程序智能编制与优化功能。
2)刀具、夹具及工件智能动态监管功能。
3)工艺参数智能决策与优化功能。
4)基于数控程序虚拟加工功能。
5)节能调度功能。
3. 智能维护功能
智能机床在维护时,具有自主故障检测和智能维修维护以及远程智能维护,同时具有自学习和共享学习的能力。
1)智能故障诊断功能。
2)故障知识自学习与共享学习功能。
3)基于3D的故障维修拆卸与组装功能。
4)故障远程维修自修复功能。
5)机床可靠性评估与故障智能预测功能。
4. 网络集成与网络协同功能
从生产过程的全局出发,通过网络化和集成化的方式,具有制造过程相关信息的采集、资源的配置、车间生产组织、过程的管理和功能的协同能力,实现制造过程的网络化和可视化管理。
1)网络通信功能。
2)制造信息采集传输功能。
3)加工过程追踪管理功能。
4)产品质量管理、数据追溯功能。
5)车间制造过程和制造资源的优化运行功能。
6)生产调度和过程管理功能。
7)远程实时监控与诊断功能。
8)制造信息共享和语义集成功能。