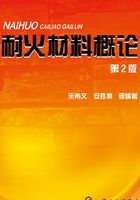
2.4 耐火材料的成型
借助外力和模型将坯料加工成为具有一定尺寸、形状和强度的坯体或制品的过程叫成型。成型是耐火材料生产过程的重要环节。通过成型可获得结构均匀、致密并具有一定强度的砖坯。耐火制品的成型方法很多,按坯料含水量的多少可分为半干法(坯料水分5%左右)、可塑法(水分15%左右)和注浆法(水分40%左右)。耐火制品生产中可根据坯料的性质、制品的形状、尺寸和工艺要求来选用成型方法。
一般的耐火制品多采用半干法成型。半干法成型由于坯料水分较低,可使用压砖机压制,压制后的坯体强度高,可随意搬动而不易损坏。半干法成型适用于熟料含量不同的(50%~100%)坯料,可塑法成型适用于制造大型或复杂的制品,注浆法则适用于生产空薄壁的各种类型的高级耐火制品。
不论采用何种方法,成型后的耐火制品坯体均应满足下列要求:①形状、尺寸和精度符合设计要求;②结构均匀、致密,表面及内部无裂纹;③具有足够的机械强度;④符合预期的物理性能要求。
2.4.1 机压成型法
机压成型法是使用压砖机将坯料压制成坯体的方法。一般机压成型均指含水量为4%~9%的半干料成型方法。常用的设备有摩擦压砖机、杠杆压砖机和液压机等。
成型过程实质上是一个使坯料内颗粒密集和空气排出、形成致密坯体的过程。为获得致密的坯体,必须给予坯料足够的压力。压力的大小应能够克服坯料颗粒间的内摩擦力、坯料颗粒与模壁间的外摩擦力以及由于坯料水分、颗粒及其在磨具内填充不均匀而造成的压力分布不均匀性。这三者之间的比例关系取决于坯料的分散度、颗粒组成、坯料水分、坯体的尺寸和形状等。虽然压力与坯体致密化的关系由若干理论公式可供计算,如坯体气孔随压力成对数关系而变化等,但通常用试验方法近似地确定坯体所需的单位面积压力,并以此决定压砖机应有的总压力。
机压成型除对坯料水分有一定要求外,对其颗粒度也有一定要求,如应有合理的粒级配比,堆积密度尽可能大。一般临界粒度为3~5mm,小于0.088mm的细粉含量应在35%~45%范围内。
机压成型的砖坯最易出现的缺陷是层裂和层密度现象。层裂是在加压过程中形成的垂直于加压方向的层状裂缝。坯料水分过高、细粉过量、结合剂过少及压力过高都会导致层裂的产生。因此生产中必须对这几方面的参数加以控制。层密度现象即成型后砖坯的密度沿加压方向逆变。由上方单方向加压的砖坯一般是上密下疏,同一水平面上是中密外疏。这是由于坯料颗粒间的摩擦力和坯料与模壁间的摩擦力而造成的压力递减所致。采用双面加压及在模具四壁涂润滑油降低外摩擦力的方法,可减少此种现象并降低坯体的气孔率。
成型设备的选择要根据制品的质量要求、形状、尺寸和生产数量等进行综合考虑。一般像加热炉用砖这样形状简单、数量多、质量要求一般的制品,可选用生产效率较高的杠杆压砖机;质量要求较高的制品可采用公称压力不低于3000kN的摩擦压砖机;厚度较大或形状复杂而生产量大的制品,采用高冲程摩擦压砖机成型。当制品规定了显气孔率下限指标时,应选用压力较小的压砖机。
机压成型设备中,使用较多的是摩擦压砖机,常用的摩擦压砖机有公称压力(kN)为700、1600、2000和3000等,高压力的摩擦压砖机有公称压力(kN)为6000、7500、8000、10000、20000或更高。使用摩擦压砖机压制砖坯时,应严格执行先轻后重的操作方针,以利于坯料中空气排出。通过控制加压次数和最大冲击力来保证砖坯的质量。由于摩擦压砖机能量的传递是借助摩擦轮进行的,易因环境条件(如湿度等)的影响而波动。用液体传递能量的液压机的压力比较稳定,不受外界条件的影响,便于控制。液压机加压一般没有冲击现象。因此,利用摩擦压砖机时,物料承受的压力一般大于其公称压力,而使用液压机时,物料承受的压力小于其公称压力。利用浮动加压、液压机可较方便地实现双面加压,减少层密度现象。在实施压机自动化方面,液压机较为方便。为了便于坯料内空气的排出和石墨料的压实,在高吨位的压力机中增设抽真空装置。
成型模具由金属制成,要求模具具有较高的耐磨、耐压和好的抗冲击性能。模具的材质主要是碳素钢、合金钢等。对设计和制作模具有以下要求。
(1)缩放尺率。为保证坯体在干燥和烧成后有准确的外形尺寸,根据不同砖种和坯料,通过实验来决定成型时的缩放尺率。除硅砖外,大部分砖在干燥或烧成后体积均会收缩,所以在设计模型时应适当放大尺寸。一般的黏土砖、高铝转、镁砖等缩放尺率为0.5%~2.5%。硅砖因在烧成时体积发生膨胀,制造模具时应缩小尺寸,一般缩尺率为3%~4%。
(2)锥度。模板安装应有锥度,以便于脱模。因此模具应上口大,下口小,锥度约为千分之五。
(3)厚度超过150mm的制品,应考虑使用双面加压模具。
(4)坯料在受压时有一定的压缩比,在设计模具时应按压缩比决定其高度,一般压缩比约在2之内。
2.4.2 其他成型法
2.4.2.1 可塑成型法
可塑成型是指用可塑泥料制成坯体的方法。在耐火材料中,软质黏土加水调和后具有可塑性。可塑在一定范围内随水分的增加由弱变强,因此,用于可塑性法的泥料应含相当数量的软质黏土(一般为40%以上)和一定的水分(一般为16%以上)。
可塑性所用设备多为挤泥机和再压设备,有时用简单工具以手工进行,称为手工成型法。采用手工成型时,坯料有时不含黏土,加镁砖及硅砖用卤水或石灰乳作为成型塑化介质,这时手工成型料的含水量也较低,水分含量近于半干成型坯料含水量的上限。
在用挤泥机生产时,将制备好的泥料放入挤泥机中,挤成泥条,然后切割,按所需尺寸制成毛坯,再将毛坯用压砖机压制,使坯体具有规定的尺寸和形状。坯料的含水量与原料性质、制品要求有关。水分可按坯料中软质黏土的多少及其可塑性强弱进行调整。挤泥机的临界压力与坯料的含水量有关,水分越大,挤泥机的临界压力越低。可塑成型法多用来生产大型或特异型耐火制品。与半干法相比,其缺点是坯体水分大,砖坯强度低,外形尺寸不准确,干燥过程复杂,收缩有时达10%以上。因此,在耐火制品生产中,除部分制品外,一般很少采用。
2.4.2.2 注浆成型法
注浆用浆料为含陶瓷粉料的悬浮液,它具有一定的流动性,将悬浮液注入模腔,形成具有一定形状的毛坯,这种方法称为注浆成型。
为了保证注浆坯体的质量,注浆用浆料必须满足以下要求:①黏度小,流动性好,以保证料浆充满型腔;②料浆稳定性好,不易沉淀与分层;③在保证流动性的前提下,含水量应尽量少,以避免成型和干燥后的收缩、变形、开裂;④触变性要小,保证料浆黏度不随时间而变化,同时在脱模后坯体不会在外力作用下变软;⑤料浆中的水分容易通过已形成的坯体被模壁吸收;⑥形成的坯体容易从模型上脱离,并不与模型反应;⑦尽可能不含气泡,可在浇注前对料浆进行真空处理。
可采用空心注浆和实心注浆的方法进行注浆成型。空心注浆又叫单面注浆,所使用的石膏模没有型芯。将调制好的陶瓷料注满模型后,经过一段时间待模型内壁黏附一定厚度的坯体后将多余料浆倒出,使坯体形状在模型内固定下来。这种方法用于浇注小型薄壁产品;实心注浆是将陶瓷浆料倒入外模与型芯之间,坯体的外部形状的外部形状由外模决定。这种方法适用于内外形状不同和大型、厚壁的产品,由于模型从两个方向吸收水分,靠近模壁处坯体较致密,坯体中心部位较疏松,因此要求浆料的浓度和注浆操作都比较严格。
为了提高注浆浇注速度和坯体的质量,还可以采用压力、离心注浆和真空注浆等新工艺方法,压力注浆是采用重力或压缩空气将浆料注入模型。压力注浆可以缩短吸浆时间,减少坯体的干燥收缩,并减少脱模后坯体的残留水分;离心注浆是在模型旋转的情况下,将料注入模型,在离心力的作用下料浆紧贴模壁坯体,这种方法得到的坯体厚度均匀,变形少。真空注浆可以在石膏模外抽取真空,也可以在真空室中负压下注浆,都可加速坯体成型。真空注浆可减少气孔和针眼,提高坯体强度。
2.4.2.3 热压铸成型
热压铸是注浆法之一,是一种生产陶瓷制品和特种耐火材料的方法。热压铸法一般以有机结合剂作为分散介质,以硅酸盐矿物粉为分散相,在一定温度(70~85℃)下,配制成浆料,然后在金属模型中成型制品。这种方法适用生产形状复杂,具有特殊要求的小件制品,还适用于生产可塑性小的材料。其半成品机械强度高,可用机床车削及钻孔加工;可以省掉石膏模型和干燥工序,设备简单,易实现机械化。热压铸的工艺流程如下。
(1)制备浆料。分散相是根据不同产品所配制的粉状坯料,为分散相,应充分干燥;结合剂为分散介质,常以热塑性有机物,如石蜡、地蜡以及他们的溶合物作为结合剂,其中以石蜡使用最多。油酸是结合剂的外加部分,它是一种表面活性物质,可以在保证流动性的前提下,大大减少石蜡的用量。石蜡的用量太多,制品的收缩大,但油酸的用量也不能太多,否则会形成多分子吸附层,产生凝聚现象,颗粒沉淀,影响料浆的均匀性和流动性。常用的结合剂配比为石蜡∶油酸=100∶(4~8)(以质量计)。
料浆结合剂的用量,必须严格控制,用量多料浆黏度下降,稳定性、浇注性都好,半成品强度大,但浇注和烧成后的收缩大,体积密度小,较适宜的范围是干料粉∶结合剂=100∶(6~8)。
(2)制成粉饼。为了便于储放混好的料浆,可将其倒入容器中(如搪瓷盘)冷却固化,冷却过程中使其振动,有利于气泡逸出。制好的饼料应置于清洁干燥处。
(3)热压铸成型过程浆料饼加热熔化,并不断地均匀搅拌,使气泡逸出,熔化的料浆倒入热压铸成型机。热压铸时的工作压力依据注件尺寸大小而异,一般在0.4~0.6MPa压力范围内,工作温度50~60℃。
影响热压铸工艺的主要因素是料浆温度、注模气压、稳定时间(即压缩空气持续时间)、浇注速度及铸件冷却速率。
热压铸成型后,坯体还要经过脱蜡、素坯加工和烧成等工序。
热压铸常见的缺陷包括:①温度过低、流动性不够、压力偏低、保压时间不够所产生的欠注(模型未充满);②温度过高、进料口太小,脱模过早所产生的凹坑现象;③温度过低,流动性较差,模具排气不彻底所产生的坯体表面皱纹;④浆料除气不彻底,流动性与压力过大,以及模具设计不合理所引起的气泡;⑤模具过热,脱模过早产生的形变,模具温度过低,脱模过晚等引起的开裂。
脱蜡过程时间过长,易产生废品,应特别小心。
2.4.2.4 挤压成型法
挤压成型是指将可塑料用挤压机的螺旋或活塞挤压向前、通过机嘴成为所要求的各种形状。挤压成型适宜成型各种管状产品、柱状产品和断面规则的产品(如圆形、椭圆形、方形、六角形等),也可用来挤制长100~200mm,厚0.2~3mm的片状膜,半干后再冲制成不同形状,或用来挤制100~200孔/cm2的蜂窝状、筛格式穿孔制品。挤压成型具有污染少,效率高,操作易于自动化,可连续生产等优点;但机嘴结构复杂,加工精度要求高,同时由于溶剂和塑化剂加入较多,坯体干燥与烧成时收缩大。
挤压时,过大的机制压力将产生大的摩擦阻力,设备负担重;压力过小则要求可塑料含水量大,会造成坯体强度低、收缩大。挤制压力主要决定于机嘴的锥角,锥角大,阻力大,需要更大推力;锥角小,阻力小,挤出毛坯不致密,强度低。为了保证坯体的光滑和质量均匀,机嘴出口处有一定型带,其长度与机嘴出口直径有关,一般为直径的2~2.5倍。定型带长,内应力大,坯体易出现纵向裂纹;定型带短,挤出的坯体会产生弹性膨胀,导致出现横向裂纹,且挤出的坯料容易摆动。当挤制压力固定后,挤出速率主要决定于转速和加料速度,坯体的弹性后效在挤出速率过快时易造成坯体变形。在挤出管子时,壁厚与管径有一定比例关系,过薄的管壁易变形,表2-2为参考用的挤压成型时管径与壁厚的关系。
表2-2 挤压成型时管径与壁厚的关系

挤压成型要求粉料粒度较细,外形要圆,以长时间小磨球球磨的粉料为好;同时要求塑化剂用量要适当,否则影响坯体质量。
挤压成型易出现的缺陷如下:①塑化剂加入后混炼时混入的气体会在坯体中造成气孔或混料不匀造成挤出后坯体断面出现裂纹;②坯料过湿,组成不均匀或承接托板不光滑造成坯体弯曲变形;③型芯和机嘴不同心造成管壁厚度不一致;④挤压压力不稳定,坯料塑性不好或颗粒定向排列易造成坯体表面不光滑。
2.4.2.5 等静压成型
等静压成型是指在常温下对密封于塑性模具中的粉料各个方向同时施压的一种成型工艺技术。与前述常规机械模压相比,在等静压过程中粉料颗粒与塑性包套接触的表面在成型期间无相对位移,不存在模壁摩擦作用,即使对于塑性包套中有钢性模件的情况,其粉料颗粒与刚性模表面之间的摩擦作用也远远低于常规模压。因此认为,在等静压过程中,成型压力不受或很少受到模壁摩擦力的抵消,成型压力通过包壁在各个方向作用于粉料,因此所得到坯体密度比常规模压高,而且均匀。
等静压成型分湿袋法和干袋法两种。对于湿袋法,成型前在压机外对模具装粉组装,抽真空密封后放入高压缸中,直接与高压液体介质接触,成型后从高压缸中取出模具,脱模得到坯体。其操作工序多,适用于生产多品种、形状复杂、产量小、大型制品;对于干袋法,成型前弹性模具直接固定在高压缸内,并用带孔钢罩支撑,粉料直接装入干袋模中,如果需要排出粉料中的气体,可采用振动装置或真空泵,加压时液态介质注入缸内壁与模具外表面之间,对模具各向同时均匀加压。干袋法适合生产形状简单、批量大的小型产品。我国自制和引进的等静压机多数采用湿袋法,目前设备向大型化、高压化方向发展。
2.4.2.6 振动成型法
利用振动作用使泥料制成坯体的成型方法。振动成型方法的原理是物料在频率很高(一般为3000~12000次/min)的振动作用下,质点相互撞击,动摩擦代替质点间的静摩擦,泥料变成具有流动性的颗粒,在自重和外力作用下逐渐堆集密实形成致密的粉体。
振动成型时,由于振动输出的能量、颗粒具有三维空间活动的能力,颗粒密集并填充于模型的各个角落而将空气排挤出去。因此,甚至在很小的单位压力下也能得到密度较高的制品。在多种制品的成型中,振动成型能够有效代替重型的高压压砖机,如杠杆压砖机和水压机等,大大提高了劳动生产率,减轻了劳动强度。振动成型也适用于成型密度相差悬殊的物料和成型易碎的脆性材料。由于成型时物料颗粒不受破坏,所以适于成型易水化的物料,如焦油白云石、焦油镁砂料等。
振动成型具有下列优点:设备结构简单,易于自制,造价低,所需动力较小,操作简单;在正确选择工艺因素和振动成型参数的条件下,所成型的砖坯密度较高且比较均匀,气孔率较低,耐压强度高,外形规整,棱角完好;采用振动成型时,对砖模的压力和摩擦力很小,故对模板的材质要求不高。但是,振动成型设备的零部件都应具有较高的强度和刚度,要采用抗振基础;振动成型设备的噪声较大,必须采用隔声设备。
振动成型设备的结构形式有很多种,常用的有振动台式、带内部震动器和表面振动器等,其中以加压振动式最简单实用。加压振动即在振动台上的泥料上方再施加一个向下的压力,使泥料不单纯受到一个振动作用,而且还受到一个从泥料下方向上的有一定频率的冲击力,更有利于坯体的密实。
采用振动成型时,工艺因素和振动过程参数对制品性能影响很大,实验表明,振动成型时,振动频率与振幅、结合剂种类、结合剂数量、水分、颗粒级配、加压压力等对制品的性能都有影响。
2.4.2.7 捣打成型法
捣打成型是用捣锤捣实泥料的成型方法。捣打成型通用于半干泥料,采用风动或电动捣锤逐层加料捣实。
用风动捣锤时,动力为压缩空气。空气压缩机给出的压力为0.7~0.8MPa时,在端面积为60cm2的捣锤作用下,能够在坯料单位表面积上受到使泥料足够致密的压力;在空气压缩机生产率为10m3/min的情况下,可同时安排6~7名工人操作,一个气锤的生产率可达200kg/h。
捣打成型既可在模型内成型大型和复杂型制品,也可在炉内捣打成整体结构,捣打的模型可用木模型或金属模型。
捣打成型的泥料水分一般在4%~6%范围内,在生产大型制品时,泥料的临界粒度应比机压成型适当增大,如6~9mm,以提高坯体的体积密度。捣打成型由于是分层加料,在加料前必须将捣打坚固的料层扒松,然后进行加料。
捣打成型操作劳动强度大,使用悬挂式减震工具可适当改善操作条件。
2.4.2.8 热压成型法
热压成型法是在加热同时加压的条件下,将泥料成型并烧结成制品的方法。热压工艺是把泥料的成型和烧成结合为一个过程,这种方法在冶金工业中用于粉末冶金已有较长的历史,在耐火材料生产中已逐步推广应用。
热压法的特点在于可获得致密度很高的特殊制品,其密度值几乎可达理论值,在高温下加压有助于坯体泥料颗粒之间的接触与扩散,从而降低烧结温度,缩短烧结时间。
热压设备采用液压机和石墨模型。石墨模型可经受高温并在高温下承受较高的压力。模具的加热可用感应线圈或电阻加热,一般使用高频感应热压电炉,泥料装入模具内进行热压,温度可达1850℃或更高一些,压力范围为25~50MPa。
在耐火材料工业中,热压法多用于纯氧化铝制品,如氧化铍、氧化镁、氧化钙、氧化铝以及其他难熔化合物制品的制造。
2.4.2.9 熔铸成型法
熔铸成型法是指物料熔化后浇注成制品的方法。熔铸法制造耐火制品一般使用配有调压变压器的三相电炉,砖料在电弧炉内熔化,然后将溶液倒入耐高温的模型中,经冷却、退火后切割成所需形状的制品。
熔铸耐火材料具有晶粒大、结构致密、机械强度高、耐侵蚀等一系列优良性能。可以制造大尺寸的制品,主要用于玻璃熔窑、玻璃工业用熔铸耐火材料,主要有锆刚玉质和纯刚玉质的耐火制品。