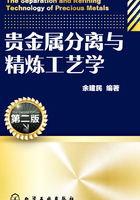
3.3 金的电解精炼[4~6]
目前,电解精炼法仍是金精炼的主要方法,并往往是大中型企业的首选方案。用于电解的原料一般含金在90%以上。如火法氯化法得到的品位大于99%的粗金,铜、铅阳极泥经银电解处理所得的2次黑金粉、金矿经金银分离所得的粗金粉以及其他废料经处理后所得的粗金等。将粗金配以硝石、硼砂熔铸成阳极,经电解得到纯金。
目前,国内普遍采用电解提纯,将粗金铸成阳极板,利用电流的作用使金在阳极上溶解,在阴极上选择析出而达到提纯的目的。国内采用此方法的厂家有成都长城精炼厂、内蒙古乾坤精炼厂、沈阳冶炼厂综合回收车间等。该方法国内外已相当成熟,但该方法存在如下缺点:一是电解金品位要达到国家1号金,阳极金品位一般达到99.5%以上,也就是说该方法适于处理品位在99.5%以上的粗金,对于品位小于99.5%的粗金必须预处理达到99.5%以后才能进行电解;二是该方法流程中积压黄金较多。
3.3.1 金电解精炼原理
金电解精炼,以粗金作阳极,以纯金片作阴极,以金的氯化配合物水溶液和游离盐酸作电解液。电解过程可近似地用下列电化系统表示:
阴极 电解液 阳极
Au(纯)︱HAuCl4+HCl+H2O︱Au(粗)
氯金酸是强酸,完全电离:
HAuCl4H++[AuCl4]-
[AuCl4]-部分电离为Au3+:
[AuCl4]-Au3++4Cl-
但其电离常数很小,,因此,可粗略认为金在电解液中以[AuCl4]-状态存在。
在水溶液中[AuCl4]-发生水解:
[AuCl4]-+H2O[AuCl3(OH)]-+H++Cl-
然而,在酸性溶液中实际上不会发生水解。因此,可以认为电解液中金以配阴离子[AuCl4]-形式存在。
3.3.1.1 阴极反应
阴极发生金还原,其主要反应是:
[AuCl4]-+3eAu+4Cl-
该反应的标准电势为+0.99V,因此,与这一反应竞争的氢还原反应实际上被排除。
由于电解液中还有[AuCl2]-,故在阴极还有一价金的还原反应:
[AuCl2]-+eAu+2Cl-
该反应的标准电势为1.04V,与3价金很接近,有同时放电的可能。但增大电流密度就可减少1价金离子的生成。
3.3.1.2 阳极反应
阳极金溶解转入溶液:
氯和氧的标准电势比金的电势高得多:
所以在正常电解条件下,在阳极不可能析出氯和氧。但是,金典型的最重要的阳极行为是它的钝化倾向。当金转化为钝化状态时,阳极停止溶解。阳极的电势向正电势方向移动,直到可析出氯气的数值。由于O2在金上的超电压高于Cl2,故先析出Cl2。钝化现象极为不利,在阳极不是发生金的有效溶解过程,而是发生氯离子氧化的有害过程,使电解液中金贫化,并毒化车间空气。
图3-4为金的阳极溶解极化曲线图。由数据可见,金转为钝化状态取决于电解液的温度和盐酸的浓度,特别是盐酸的浓度。例如,如果在0.1mol/L HAuCl4溶液中不含游离盐酸,在温度为20℃的条件下,电流密度很低(图3-4,曲线6),金开始钝化,而在同样溶液中,含1mol/L HCl,甚至在电流密度为1500A/m2时(图3-4,曲线1),金仍然活性很强。因而,为避免阳极钝化和析出氯气,电解液必须有足够高的酸度和温度。在这种情况下,使用的阳极电流密度越大,电解液中的盐酸的浓度应该越高,温度也应该越高。提高盐酸的浓度和温度,不但可消除金的钝化,而且可提高电解液的电导率,因此可减少电能消耗。

图3-4 不同HCl浓度和温度下0.1mol/L HAuCl4溶液中金的阳极溶解极化曲线
1—1mol/L HCl,20℃;2—0.1mol/L HCl,80℃;3—0.25mol/L HCl,20℃;4—0.1mol/L HCl,50℃;5—0.1mol/L HCl,20℃;6—不加HCl,20℃
电解金的另一个重要特性是阳极溶解时金不仅以阴离子[AuCl4]-的形式转入溶液,而且也以阴离子[AuCl2]-的形式转入溶液:
由于1价金的电化当量比3价金大,按3价金计算的阴极电流效率会出现超过100%的现象。阴离子[AuCl4]-和[AuCl2]-之间的平衡关系为:
但这一歧化反应的平衡常数相当小,实际上阳极生成的[AuCl2]-的浓度超过了平衡值,上述不成比例的反应平衡式向右移动,同时,部分金呈细粉状沉入阳极泥中。从阳极泥中回收金需要增加工序,因此,应尽力防止金粉生成。实践证明,进入阳极泥的金量随着电流密度的增高而减少。
3.3.2 金电解时杂质的行为
金电解精炼的阳极板是一种含有多元素的合金。随着阳极金的溶解,阳极中杂质的行为也各不相同。金电解精炼过程中,阳极上凡是比金更负电性的杂质都电化溶解而进入电解液,只有铂族金属中的铑、钌、锇、铱等不溶而进入阳极泥中。进入电解液中的杂质,有些因浓度不高,一般也不易在阴极上析出;有些(如PbCl2)在电解液中的溶解度低而沉淀到阳极泥中;铜离子的浓度一般较高,有可能在阴极析出,影响金的质量,因此,阳极中的铜宜控制在不超过2%;铂、钯进入电解液后,积累到一定程度,就应处理加以回收。金电解精炼的电解液中杂质的最高允许含量见表3-3。
表3-3 金电解精炼的电解液中杂质的最高允许含量

阳极中最有害的成分是银。在阳极中的银成为氯化银壳黏附在阳极或是脱落进入阳极泥中,氯化银一般可视为不溶于电解液的化合物,但是电解液中的含酸量较高时,氯化银也会部分溶于溶液中,当溶液稀释后,氯化银又自然析出。氯化银在盐酸中的溶解度与温度的关系列于表3-4。当阳极中含银不大于1%时,生成的氯化银颗粒非常细微,这种氯化银不易沉淀而悬浮在电解液中,对阴极质量较为有害。当阳极中含银在3%~4%时,此时生成的氯化银比较容易脱落进入阳极泥中。当阳极中含银大于10%以上时,所生成的氯化银将附着在阳极板上,使阳极金产生钝化,妨碍阳极金的继续溶解,并使阳极析出氯气,同时导致电解液中金的贫化,生产速度减慢,这种情况必须采用机械或手工的方法将阳极上的氯化银壳除掉。
表3-4 氯化银在盐酸中的溶解度

为了解决银的危害,金电解精炼时,往电解槽中输入直流电的同时输入交流电,形成非对称性的脉动电流。脉动电流的变化如图3-5所示。一般要求交流电的I交应比直流电的I直大,其比值为1.1~1.5,这样得到的脉动电流I脉,随着时间的变化,时而具有正值,时而具有负值。当其达到峰值时,阳极上瞬时电流密度突增,此时,阳极上有大量气体析出,AgCl薄膜即被气泡所冲击,变疏松而脱落;当电流为负值时,电极的极性也发生瞬时的变化,阳极变为阴极,则AgCl的生成将受到抑制。使用脉动电流,不仅可以克服AgCl的危害,还可提高电流密度,从而减少金粉的形成,还可以提高电解液的温度。脉动电流的电流和电压,可用下列公式计算:

图3-5 脉动电流变化图
较新的方法介绍如下:
①使用非对称交流电源,该电源为交流电正半周导通,负半周小部分导通并可调,适用于含银较高的阳极。
②使用周期自动换相金电解装置(中国专利ZL 93229729.3),应用矩形方波电流,先正向导通数秒至数十秒,再反向导通数秒来消除钝化。此装置投资少,操作控制方便,较适用于原料含银较低的中小型黄金矿山及首饰加工厂。
电流的周期反向(或称换向)电解技术是1949年首先用于电镀生产的,它使镀件获得了光洁的高质量镀层。它是在正常供电条件下,每隔一定时间(50~150s)将正极供入的电流自动切换至负极,经2~4s再自动切换至正极,如此来回换向,一台供电设备每年需频繁换向数十万次乃至数百万次。因而,此项技术直至大功率可控硅整流器和无触点快速换向开关问世后才于1969年先后在日本、赞比亚、美国和南非几家大型铜厂的电解中获得应用。我国的周期反向电解技术试验始于1971年。1973年在原沈阳冶炼厂进行了电流强度6400~7400A(电流密度178~230A/m2)、正向供电140~150s、反向供电3~4.2s的铅电解扩大试验。试验结果:电流效率为92.76%~93.37%,电铅产品表面光洁、质量良好。

图3-6 周期自动换向时间和电流波形示意图
周期反向电解的电流效率虽取决于正极供入电流,负极换向瞬间供入电流属“无用功”,但它可将阴极上生长的尖形粒子反溶除去,防止极间短路,并产出质量良好的电解产品。且通过电流的频繁换向和来回振荡可防止浓差极化,并使阳极表面厚硬的阳极泥层疏松脱落,防止阳极钝化。为此,东北大学黄金学院于20世纪90年代开展了周期反向技术用于金电解的试验。结果证明它可替代交直流重叠供电的沃尔维尔法,不需重叠交流电流。供入直流电流的波形变化如图3-6所示,设备及其连接示于图3-7。图中周期换向整流器可在正向3~150s、负向1~40s间自由调整。电解槽为聚丙烯硬塑料槽。电解液由蛇形玻璃管经泵送入的热水间接加热。由感温器测定电解液温度,并通过控温仪自动控制热水供应泵的关停和启动,以此来达到电解要求的温度。

图3-7 周期自动换向金电解装置
1—周期自动换向整流器;2—导电母线;3—阳极;4—阴极;5—感温器;6—自动温度控制仪;7—电解槽;8—加热玻璃管;9—胶管;10—电热自动恒温水浴;11—泵
1—周期自动换向整流器;2—导电母线;3—阳极;4—阴极;5—感温器;6—自动温度控制仪;7—电解槽;8—加热玻璃管;9—胶管;10—电热自动恒温水浴;11—泵
由于本工艺历时尚短,其工艺和设备尚需不断开发使之更趋完善。
我国目前黄金精炼采用的设备主要有GDA系列、GDF系列、GDJ系列、GDS系列和KGDS系列的可控硅整流器装置。其中,K表示硅可控成套;G表示硅成套;D表示电解或电镀用;F表示元件风冷;S表示元件水冷;J表示元件油浸冷却;A表示元件自然冷却。部分国产电解用硅整流器和可控硅整流器列于表3-5。
表3-5 部分国产电解用硅整流器和可控硅整流器

金电解精炼操作条件实例示于表3-6。
表3-6 金电解精炼操作条件实例

3.3.3 金电解精炼实践
3.3.3.1 电解液的制备
制备金电解液的最好方法是电解法,俗称电解造液。另外,还可使用王水溶解法。
①隔膜电解造液法 这种方法是在与金电解相同的槽中,采用与金电解基本相同的技术条件进行的,其最大不同点是纯金阴极很小且装于未上釉的耐酸素瓷隔膜坩埚中(图3-8)。

图3-8 隔膜电解装置
1—阳极;2—阴极;3—隔膜;4—电解液;5—电解槽
此法广泛应用于工业生产中。使用25%~30%的盐酸液,在电流密度为1000~1500A/m2和槽电压不大于3~4V条件下,可制备出含金380~450g/L的浓溶液。
某厂电解造液是在电解槽中加入稀盐酸(化学纯盐酸或蒸馏盐酸),槽中装入粗金阳极板,在素瓷隔膜坩埚中装入105mm×43mm×1.5mm(厚)的纯金阴极板。素瓷坩埚内径为115mm×55mm×250mm(深),壁厚5~10mm。坩埚内的阴极液为1:1的稀盐酸。电解槽内HCl:H2O=2:1,阴极液面比电解槽阳极液面高5~10mm,以防止阳极液渗入阴极区。
电解造液的条件通常是电流密度2200~2300A/m2,槽电压2.5~4.5V,重叠交流电为直流电的2.2~2.5倍,交流电压5~7V,液温40~60℃,同极中心距100~120mm。当接通电流时,阴极上开始放出氢气,而阳极则开始溶解,造液44~48h,即获得密度为1.38~1.42g/m3、含金300~400g/L(延长周期最高可达450g/L)、含盐酸250~300g/L的溶液,经过滤除去阳极泥后,贮存在耐酸瓷缸中备用。作业终止后,取出坩埚,阴极液集中进行置换处理,以回收可能穿透坩埚进入阴极液中的金。
鉴于金价昂贵,为提高金的直收率,使金不致积压于生产过程中,某些厂曾使用含金95~120g/L、盐酸120~150g/L的电解液。
②均质阴离子交换膜造液法 隔膜电解法造液,除了采用素瓷隔膜坩埚外,还可采用阴离子交换膜。阴膜M886A的主要化学成分是带有氨基功能基团的高分子电解质(R+Cl-),由于阴膜的高分子氨基固定基团(即R+)对电解液中的正电荷金离子有相斥作用,可以阻止金离子向阴极区迁移,使阳极区的造液效率提高。用M886A过氯乙烯弱酸性均质阴离子膜粘贴在硬聚氯乙烯框架上,黏合剂由聚氨酯胶水和过氯乙烯粉溶化于环己酮饱和溶液中制成的。阴离子膜与素瓷隔膜坩埚性能比较见表3-7。
表3-7 阴离子膜与素瓷隔膜坩埚性能比较

试验得出如下结论。
a.使用阴膜消除了在使用素瓷隔膜坩埚时在阴极产生金泥的缺陷。阴膜具有选择性,它阻止了金离子在电解过程中进入阴极,因此,在阴极上很少有金泥析出。素瓷隔膜坩埚的孔隙虽小,渗透差,阻力也大,但还不能完全阻止金离子渗透到阴极区产生金泥。金泥清除困难。相反,阴膜无此缺陷,故可提高成品产出率。
b.素瓷隔膜坩埚由于它本身壁厚,在孔隙中渗进了金粉,回收有困难。而阴膜则无此缺陷。即使阴膜黏附少量的金粉,也可焚化回收,而素瓷隔膜坩埚则无此优点。因此,使用阴膜减少了黄金损耗。
c.素瓷隔膜坩埚的电阻比阴膜大。使用阴膜的槽电压比使用素陶罐低(槽电压降低10%以上),液温相应也低,减少电能的损耗。
d.使用阴膜的盐酸蒸气量小,环境污染少,操作条件好。
③王水溶解造液法 将还原的金粉加王水溶解而制得电解液。一份金粉加入一份王水,经溶解后过滤除去杂质。为了除去溶液中的硝酸通常在金粉全部溶解后,继续加热赶硝酸以使其分解成二氧化氮而被除去。在前苏联,过去多使用王水造液,南非和日本现今仍多采用之。此法的优点是速度快,但溶液中的硝酸根不可能完全被排除。用此溶液进行电解,由于硝酸根离子的存在,会使电解过程中出现阴极金反溶解的不利现象。
一般常用氯化物电解液,亦有的用王水电解液。如乌兹别克斯坦的穆龙陶金矿因含银和杂质较高,多年的生产实践说明:采用王水电解法(工作电解液含Au 180~200g/L、HCl 110~140g/L,95~110g/L),可以处理低品位的杂质含量较高的阳极金属。该矿的粗金中的杂质是在炉料熔炼时除去的,银留在阳极金属中,电解时进入阳极泥再用分离熔炼法回收。当阳极组分含量(%)为:Au 70~90、Ag<12、Cu<20时,阴极金纯度为99.99%,但槽电压较高(2.2V)、电流效率较低(换算成Au3+,约比氯化物电解法低10%),同样条件下比氯化物电解法的生产能力低8%~10%,滞留的金达20%~25%。
无论是素瓷隔膜坩埚造液还是隔膜造液,更换后的带金的素瓷隔膜坩埚或阳离子隔膜的再处理回收,都会导致部分黄金的积压和损耗。近几年新开发了一种带有冷凝回流装置的密闭玻璃反应釜,在该反应釜中采用化学溶解法进行造液。为加快造液的速率,采用了新的药剂和操作方法,大大减少了赶硝时间。这种新的造液工艺和设备,取消了电解造液的回收处理含金隔膜或素瓷隔膜坩埚工序,并有效缩短了造液的周期。造液周期由原来的48h缩短到现在的6~8h。
3.3.3.2 阴极片的制作
阴极片制作可采用电解(电积)法和轧制法。
①电解法 金始极片,可用电解法制取,俗称电解造片。造片在与电解金相似的或同一电解槽中进行。电解液使用上述制备的氯化金电解液,槽内装入粗金阳极板和纯银阴极板(种板)。
电解造片通常在较低的电流密度和温度下进行,采用的技术条件见表3-8。
表3-8 电解造片的电解操作条件

先将种板擦拭干净,并经烘热至30~40℃后打上一层极薄而均匀的石蜡。种板边缘2~3mm处一般要经过粘蜡处理或用其他材料进行粘边或夹边,以利于始极片的剥离。
通电后,阳极不断溶解,并于阴极种板上析出纯金。经4~5h,即能在种板两面析出厚0.1~0.15mm、质量约为0.1kg的金片。种板出槽后再加入已备好的另一批种板继续造片。取出的种板用水洗净表面年黏附的电解液(洗涤水集中于废液贮槽中)。洗净的种板晾干后剥下始极片,始极片先于稀氨水中浸煮3~4h,后用水洗净,再于稀硝酸中用蒸汽(或外加热)浸煮4h左右,取出用水洗净并烘(或晾)干,然后剪切成规定尺寸的始极片和耳片,经钉耳、拍平,供金电解用。
②轧制法 将造好的金电解液(一般可采用王水法造液)用草酸(亚硫酸钠或硫酸亚铁)还原出金粉,金粉烘干后熔铸成片状金条,金的纯度一般为99.95%~99.99%。再将金锭用对辊轧机压制为0.1~0.2mm厚的金箔。为达到该厚度,轧制时可将金片折叠在一起,并不断退火,待达到生产要求的厚度时,采用人工将金箔分离。分离后的金箔按照生产要求的尺寸裁剪为大小合适的阴极片,在金片上部穿上金挂耳后供金电解提纯使用。
近几年来,人们普遍使用永久钛作阴极板,与传统的纯金压片作阴极相比采用钛合金板做阴极减少了纯金阴极这部分黄金的周转积压和纯金阴极制作过程中的损耗。为了顺利地从钛板上剥离阴极产品,在借鉴国外技术的基础上,采用一种特殊的导电涂层覆盖在钛阴极板上,这使操作过程大为简化。参见本书3.11.1电解法。
3.3.3.3 粗金阳极板的熔铸
电解前先将金原料熔铸成粗金阳极板。当原料为合质金或其他含银高的原料时,应在熔铸前先用电解法或其他方法分离银。
粗金阳极板一般在石墨坩埚内于柴油地炉中熔铸而成。地炉和坩埚容量的大小视生产量规模而定,一般常用60~100号坩埚。如用100号坩埚,则每锅熔炼粗金75~100kg。为提高阳极板的纯度,需往原料中加入少量硼砂和硝石,在1200~1300℃温度下熔化造渣1~2h。原料熔化后,还可根据造渣情况加入少量硝石等氧化剂进行造渣。在造渣过程中由于强烈的氧化和碱性炉渣的侵蚀,坩埚液面的部位常会受到严重侵蚀,甚至被烧穿。为此,可视坩埚情况加入适量洁净干燥的碎玻璃,用以中和碱渣来保护坩埚,并吸附液面的浮渣。熔炼造渣完成后,用铁质工具清除液面浮渣,取出坩埚,浇铸于经预热的模内。浇铸时不要把阳极模子夹得太紧,以免阳极板在冷凝时断裂。由于金阳极板小,冷凝速度快,因此除要烤热模子外,浇铸的速度亦要快。阳极板的规格各厂不一,在某些工厂为160mm×90mm×10mm,每块重3~3.5kg,含金在90%以上。待阳极板冷凝后,撬开模子,趁热将板置于5%左右的稀盐酸中浸泡20~30min,除去表面杂质,洗净晾干送金电解精炼。
3.3.3.4 电解槽
金电解精炼用的电解槽可用耐酸陶瓷方槽,也可用10~20mm厚的塑料板焊成的方槽。为了防止电解液漏损,电解槽外再加保护套槽。槽子构造及尺寸如图3-9所示。金电解精炼槽技术性能实例见表3-9。

图3-9 金电解槽(单位:mm)
1—耐酸陶瓷槽;2—塑料保护槽;3—阴极;4—阳极吊钩;5—粗金阳极;6—阴极导电棒;7—阳极导电棒
表3-9 金电解精炼槽技术性能实例

3.3.3.5 电解操作
在电解槽中,先注入配好的电解液,然后把套好布袋的阳极垂直挂入槽中,再依次相间挂入阴极片。槽内的两极是并联的,而槽与槽之间是串联的。电极挂好后再调整电解液,使液面略低于阳极挂钩。送电后要检查电路是否畅通,有无短路、断路现象,测量槽电压是否正常。待阴极析出金到一定厚度后,可取出另换新阴极片。阳极溶解到残缺时不能再用,应取出更换新阳极。阳极袋中的阳极泥,要精心加以收集。
3.3.3.6 金电解精炼的技术经济指标
金电解精炼的电解液一般含Au 250~350g/L、HCl 200~300g/L;在高电流密度作业时,含金宜高些;电解液中含铂不宜超过50~60g/L,含钯不宜超过5g/L。电解液的温度一般为50℃,如采用高电流密度可高达70℃,电解液不必加热,靠电解的电流作用即可达到上述温度。
电流密度应尽量高些,一般为700A/m2,国外有的厂高达1300~1700A/m2。如采用高电流密度,宜提高阳极品位、电解液中金和盐酸的浓度。电流效率主要指直流电的电流效率,因电金的析出是靠直流电的作用。一般工厂的阴极电流效率可达95%。槽电压与阴极品位、电解液成分和温度、极间距、电流密度等有关,一般为0.3~0.4V。电能消耗也是指直流电的单耗,即每生产1kg电金所消耗的直流电量。
在电解精炼工艺中,制约高电流密度的主要障碍是浓差极化严重,导致阴极板表面的电解液中金离子严重贫化,金在阴极板析出的物理状态恶化,电解液中的杂质离子被夹杂或还原混入产品中,从而影响产品质量。另外,高电流密度还会导致阳极钝化。减少浓差极化的措施主要是加强电解液中的离子扩散运动,国内某公司在借鉴国内外先进经验的基础上,经过不断探索完善,开发了一套结构简便、运行平稳的强化离子扩散装置,从而使高电流密度的使用得以实现。这种强化离子扩散装置有效地减少了电解液中的浓差极化现象,使阴极析出的黄金产品质量得到了更稳定的提高,并简化了控制条件。新设备投入运行以来,黄金产品质量始终保持在99.995%以上,超过了上海黄金交易所1号金所要求的质量标准。该装置也使得低浓度金电解液得以采用,金浓度由原来的240~300g/L降到100g/L左右。另外该装置还有助于清理阳极板表面黏附的阳极泥,不再需要交直叠加电流,只用单纯直流电源即可,简化了生产操作和电源结构,阳极的残极率也有所降低,由此降低了流程中金的积压。通过技术开发和生产实践,在保证产品质量的前提下,电流密度由原来的300A/m2左右提高到1000A/m2以上,精炼周期由原来的80~100h缩短到24h之内。
表3-10列出了中国某些工厂金电解精炼的主要技术经济指标,表3-11列出了日本某些铜冶炼厂的金电解精炼技术经济指标。
表3-10 中国某些工厂金电解精炼技术经济指标实例

①包括造液所消耗的直流电。
②浓度为31%的盐酸。
③金银合金至金锭的回收率。
④阳极泥至金锭的回收率。
表3-11 日本某些铜冶炼厂的金电解精炼技术经济指标

3.3.3.7 产品及其处理
(1)电金
阴极金(电金)取出后用水洗涤,去掉表面的电解液、洗涤,洗涤水不能弃去。电金在坩埚炉中于1200~1300℃下熔融,熔化后金液表面宜用适量火硝覆盖,浇铸温度为1150~1200℃,铸模预热到120~150℃,熏上一层烟灰。金锭脱模后用稀盐酸煮沸3~4h,氨水浸泡3~4h,纯水洗涤后用洁净纱布蘸酒精擦拭表面,使之光亮。金锭品位一般大于99.95%,1994年金产品国家标准(GB 4134—1994,已作废)见表3-12。我国国家质量监督检验检疫总局于2015年9月11日发布了金锭最新国家标准——GB/T 4134—2015,从2016年4月1日起实施,参见本书表10-1。
表3-12 金产品国家标准(GB 4134—1994)

注:1号、2号金的含量是以100%减去表列杂质总和而得,3号金的杂质含量不规定上限,但必须参加减量。
可用多次电解的方法制备高纯金,如用含金量>99.9%的阳极,在HAuCl4+HCl电解质中用钽片作阴极,经2次电解、硝酸煮洗,获得Au>99.999%的高纯金。
(2)残极
电解一定时间后,阳极溶解到残缺不全,称为残极,残极取出后,要精心洗刷,收集其表面的阳极泥,然后送去与2次黑金粉一起熔铸成新的阳极。
(3)阳极泥和电解废液的处理
金电解阳极泥产率一般为20%~25%,含90%AgCl、1%~10%金,通常将其返回再铸金银合金阳极板供银电解。由于氯化银的熔点低(452℃),熔炼时容易挥发损失,为此某厂将金电解阳极泥于地炉中熔化后用倾析法分离金,氯化银渣加入碳酸钠和碳进行还原熔炼,铸成粗银阳极送银电解,金返回铸金阳极。
当金阳极泥中含有锇、铱时,应先筛分阳极泥,选出锇和铱后,再回收金、银。
更换电解槽中的金电解液应先将废液抽出,并将阳极泥清出,然后洗净电解槽加入新液。废液和洗液全部过滤,获得的阳极泥洗净烘干。废液和洗液一般先用二氧化硫或亚铁还原其中的金,再加锌块置换铂族金属至溶液澄清为止。经过滤,滤液弃去。滤渣含铂族金属较高,用1:1的稀盐酸浸洗除去铁、锌后,送精制铂族金属。
当电解废液含铂、钯很高时,也可先用氯化亚铁还原其中的金,再分离铂、钯等。处理这种金电解废液也可先加入氯化铵使铂呈氯铂酸铵沉淀后,再用氨水中和溶液至pH=8~10,使贱金属水解除去,再加盐酸酸化至pH=l,钯即生成二氯二氨配亚钯沉淀。余液用铁或锌置换回收残余贵金属后弃去。
金电解过程中,如电解液中含铂、钯过高,有可能与金一道析出时,也可采用上述方法净化电解液。除去铂、钯后,溶液返回电解使用。
某厂在进行含金49.85g/L、钯4.74g/L、铂0.68g/L的金电解废液试验时,分别使用硫酸亚铁、二氧化硫和草酸还原金,金、钯和铂的沉淀率见表3-13。
表3-13 金、钯和铂的沉淀率

从表3-13中可以看出,硫酸亚铁还原金的还原率高,铂、钯的损失少;草酸最低;二氧化硫还原金的还原率虽最高,但钯的损失过大,可能是生成不溶性的钯配盐之故。还原金后的溶液尚含有少量金,再加入锌块置换,贵金属的回收率(%)分别为:Au 99.77、Pd 98.93、Pt约100。当把溶液酸度提高到0.2mol/L时,用锌还原效果会更好。如将草酸还原金的滤液不加锌置换改用甲酸还原,先将溶液pH值调至6,再加入甲酸,贵金属的回收率(%)分别为:Au 99.70、Pd 99.97、Pt 96.09。
又据某公司十多年使用锌置换法处理各种贵金属氯化液和精炼过程废液的经验证明:锌置换法是一种具有过程迅速、置换彻底、操作简便以及不需特殊设备的简便易行的可靠方法。经鼓风搅拌,最终加锌粉置换后的残液中金、铂、钯<0.0005g/L,达到了生产废弃的标准。金、铂、钯的置换回收率在99%~99.9%之间,效果是令人满意的。为了获得更好的效果,还可以采取下列措施:
a.可适当增加置换液的酸度,并鼓风搅拌,以免贵金属精矿中含锌粉过高。如锌粉过高,可于3mol/L盐酸液中加热至80~90℃搅拌除锌。
b.溶液含铜等贱金属过高时,改用铜置换。用锌或铜置换所得的贵金属精矿,均使用60g/L的硫酸高铁溶液浸出除铜。
c.含有硝酸和亚硝酸介质的溶液,锌置换法不能彻底回收其中的贵金属,应避免使用。
前苏联曾使用电解法处理金电解废液。该法是在金电解造液时,将电解废液注入阴极隔膜内,在阳极区溶解阳极的同时,废电解液中的金则于阴极上析出。析出的阴极金供铸阳极用。